Aluminium 5052 Sheet Metal Parts for Outdoor Furniture Frames
Weather-Resistant
Product Description:
Sheet metal products have several key characteristics:
1. Lightweight: Sheet metal is thin, making the products light yet
durable.
2. High Strength: Despite being thin, sheet metal offers strong
structural integrity and resistance to external forces.
3. Flexibility: It can be easily shaped, cut, and bent into various
designs, providing versatility in manufacturing.
4. Cost-Effective: Due to the material's availability and the
efficiency of the manufacturing process, sheet metal products are
typically affordable.
5. Corrosion Resistance: Depending on the metal used, many sheet
metal products are resistant to corrosion, especially when treated
or coated.
6. Customizable: Sheet metal can be tailored to specific sizes,
shapes, and functions, allowing for custom designs in various
industries.
7. Good Thermal Conductivity: Many sheet metal materials, such as
aluminum and copper, have excellent thermal conductivity, making
them suitable for heat-related applications.
These characteristics make sheet metal products widely used in
industries like automotive, aerospace, electronics, and
construction.
Simplified Manufacturing Process
Sheet metal fabrication is often simpler and more streamlined
compared to other manufacturing processes, making it an ideal
choice for producing high-quality components quickly and
efficiently. Sheet metal parts can be produced using highly
automated processes, reducing the need for manual labor and
minimizing the chances of human error.
The ability to create prototypes and scale production quickly makes
sheet metal fabrication a valuable tool for industries that require
rapid product development, such as electronics, automotive, and
medical devices. In addition, the wide availability of sheet metal
materials and the efficiency of the manufacturing process
contribute to faster turnaround times and reduced lead times for
production.
In the realm of materials science and engineering, the term
"weather-resistant" is often used to describe the ability of a
material, product, or structure to withstand the effects of various
environmental conditions. These conditions can include exposure to
sunlight, rain, snow, wind, humidity, and temperature fluctuations.
Understanding the concept of weather resistance is crucial in
numerous industries, from construction and automotive to consumer
electronics and textiles.
1. Understanding Weather Resistance
Weather resistance is not a single property but rather a
combination of several characteristics that enable materials to
endure prolonged exposure to the elements without significant
degradation. For instance, a weather-resistant material might be
resistant to UV radiation, which can cause discoloration,
brittleness, or cracking over time. It might also be
water-resistant, preventing moisture from penetrating and causing
corrosion or mold growth.
One of the key aspects of weather resistance is the material's
ability to maintain its structural integrity and functional
properties under varying weather conditions. For example, a
weather-resistant outdoor furniture piece should not only look good
but also remain strong and durable, even after years of exposure to
sunlight, rain, and temperature changes.
2. Factors Affecting Weather Resistance
Several factors determine how well a material can resist
weathering. These include:
Chemical Composition: The inherent properties of a material play a significant role.
For example, stainless steel is more resistant to corrosion than
regular steel due to its chromium content, which forms a protective
oxide layer on the surface.
Surface Coatings: Applying protective coatings can enhance weather resistance.
Paints, varnishes, and specialized coatings like UV-resistant
polymers can shield materials from the harmful effects of sunlight
and moisture.
Material Thickness: Thicker materials generally offer better resistance to
weathering, as they provide more material to withstand wear and
tear.
Design and Construction: The way a product is designed and assembled can also impact its
weather resistance. For example, sealed joints and proper drainage
systems in outdoor structures can prevent water accumulation and
subsequent damage.
3. Applications of Weather-Resistant Materials
Weather-resistant materials are essential in a wide range of
applications:
Construction: Building materials such as roofing shingles, siding, and outdoor
decks need to be weather-resistant to protect the structure from
the elements. Weather-resistant materials like treated wood,
aluminum, and certain types of plastics are commonly used.
Automotive: Vehicle exteriors, including body panels, windows, and tires,
must withstand harsh weather conditions. Weather-resistant coatings
and materials help protect against UV damage, corrosion, and
impact.
Consumer Electronics: Devices like smartphones, outdoor cameras, and smartwatches often
feature weather-resistant designs to protect internal components
from moisture and dust.
Textiles: Weather-resistant fabrics are used in outdoor clothing and gear,
such as tents, backpacks, and raincoats. These materials are
designed to repel water and resist UV degradation while remaining
breathable and comfortable.
4. Testing and Standards
To ensure that materials and products are truly weather-resistant,
they undergo rigorous testing. Various standards and certifications
exist to measure and verify weather resistance. For example, the
International Organization for Standardization (ISO) and the
American Society for Testing and Materials (ASTM) have developed
specific tests to evaluate a material's resistance to UV radiation,
water exposure, and temperature extremes.
One common test is accelerated weathering, which simulates years of
outdoor exposure in a controlled laboratory environment. This
involves exposing samples to intense UV light, high humidity, and
temperature cycles to accelerate the aging process and observe how
the material degrades over time.
5. Importance of Weather Resistance
In today's world, where environmental conditions are becoming more
extreme and unpredictable, weather resistance is more important
than ever. Weather-resistant materials not only extend the lifespan
of products and structures but also reduce maintenance costs and
environmental impact. For example, using weather-resistant
materials in construction can reduce the need for frequent repairs
and replacements, saving resources and reducing waste.
Moreover, weather resistance is crucial for safety and
functionality. In the automotive industry, weather-resistant
materials ensure that vehicles remain safe to drive even in adverse
conditions. In consumer electronics, weather-resistant designs
protect valuable components from damage, ensuring that devices
continue to function properly.
Applications:
Aluminum 6061 is one of the most commonly used aluminum alloys due
to its excellent combination of strength, corrosion resistance,
weldability, and ease of processing. It belongs to the 6000 series
of aluminum alloys, which are primarily composed of aluminum,
magnesium, and silicon. Due to its versatile properties, 6061 is
widely used in industries such as aerospace, construction,
automotive, marine, and electronics. This article will explore the
key characteristics of aluminum 6061, including its chemical
composition, physical properties, mechanical properties, corrosion
resistance, weldability, and common applications.
1. Chemical Composition
Aluminum 6061 is a heat-treatable alloy, and its chemical
composition is primarily based on aluminum, with significant
amounts of magnesium and silicon. The typical composition of 6061
aluminum alloy is as follows:
• Aluminum (Al): Balance
• Silicon (Si): 0.4–0.8%
• Iron (Fe): 0.7% max
• Copper (Cu): 0.15–0.4%
• Manganese (Mn): 0.15% max
• Magnesium (Mg): 1.0–1.5%
• Chromium (Cr): 0.04–0.35%
• Zinc (Zn): 0.25% max
• Titanium (Ti): 0.15% max
The addition of magnesium and silicon in specific proportions gives
6061 its excellent mechanical strength and corrosion resistance,
while copper provides additional strength and hardness. The
chromium content helps to enhance its resistance to stress
corrosion cracking.
2. Physical Properties
Aluminum 6061 offers a range of favorable physical properties,
including low density, high thermal conductivity, and good
electrical conductivity. Key physical properties of 6061 aluminum
include:
• Density: 2.70 g/cm³ (2700 kg/m³)
• Melting Point: 582–652°C (1080–1205°F)
• Thermal Conductivity: 151 W/m·K
• Electrical Conductivity: 40–42% IACS (International Annealed
Copper Standard)
• Specific Heat: 0.897 J/g·°C
• Modulus of Elasticity: 68.9 GPa (10.0 × 10³ ksi)
The low density of aluminum 6061 (compared to steel and many other
metals) makes it a lightweight option for applications requiring
strength-to-weight ratio. Additionally, its relatively high thermal
conductivity is useful in heat exchange applications.
3. Mechanical Properties
One of the most notable aspects of aluminum 6061 is its excellent
mechanical properties. It offers a good balance of strength,
formability, and toughness, making it suitable for a wide range of
applications. Key mechanical properties of 6061 aluminum alloy
include:
• Tensile Strength: 290 MPa (42 ksi) (solution heat-treated and
aged)
• Yield Strength: 240 MPa (35 ksi) (solution heat-treated and aged)
• Elongation: 12-17% (in 50 mm gauge length)
• Hardness: Brinell hardness 95–110 HB
• Shear Strength: 207 MPa (30 ksi)
• Modulus of Elasticity: 68.9 GPa (10.0 × 10³ ksi)
6061 aluminum alloy is a versatile material because it can be
heat-treated to achieve higher strength, making it suitable for
structural components. Its elongation values also suggest that it
is relatively ductile, allowing it to be formed into complex shapes
without cracking.
4. Corrosion Resistance
Aluminum 6061 offers good resistance to corrosion, which is one of
the main reasons it is widely used in applications exposed to
outdoor environments or marine conditions. The alloy forms a
protective oxide layer on the surface, which helps prevent further
oxidation. The key aspects of its corrosion resistance include:
• General Corrosion: 6061 is highly resistant to general corrosion
in most environments, including atmospheric conditions, water, and
many chemicals.
• Pitting Corrosion: While 6061 is resistant to pitting in most
environments, it may suffer from pitting corrosion if exposed to
chloride-rich environments, such as seawater. However, proper
coatings or anodizing can improve its resistance.
• Stress Corrosion Cracking (SCC): 6061 is generally resistant to
stress corrosion cracking in most conditions, though it may be
susceptible under certain stress conditions or when exposed to
corrosive chemicals at elevated temperatures.
• Anodizing: 6061 aluminum is easily anodized to increase its
corrosion resistance. The anodized surface is more durable,
providing additional protection in harsh environments.
5. Weldability and Workability
One of the major advantages of 6061 aluminum alloy is its excellent
weldability and workability. It can be welded using several
techniques, including TIG (Tungsten Inert Gas), MIG (Metal Inert
Gas), and arc welding. The alloy can also be easily machined,
extruded, and forged.
• Weldability: 6061 is considered one of the most weldable aluminum
alloys. It produces strong, high-quality welds, but care must be
taken during the welding process to prevent cracking. In
particular, preheating and post-weld heat treatment may be
necessary in certain cases to minimize the risk of weld defects.
• Machining: Aluminum 6061 is easy to machine, and it can be
processed with common machining tools such as lathes, mills, and
drills. Its excellent workability and surface finish make it an
attractive option for precision machining applications.
• Formability: 6061 can be easily extruded into a wide range of
profiles, including round, square, rectangular, and custom shapes.
It is also suitable for cold working operations like bending,
drawing, and rolling.
6. Applications of Aluminum 6061
Due to its unique combination of properties, aluminum 6061 is
widely used in various industries and applications, including:
• Aerospace and Aviation: The high strength-to-weight ratio,
corrosion resistance, and weldability of 6061 make it a popular
choice for manufacturing structural components of aircraft,
including wings, fuselages, and support structures.
• Automotive Industry: Aluminum 6061 is used in automotive parts
that require high strength but low weight, such as frames,
suspension components, and body panels.
• Marine Applications: In the marine industry, 6061 aluminum is
used in boat hulls, frames, and other components due to its
resistance to corrosion in seawater, making it ideal for marine
environments.
• Construction: 6061 aluminum is often used in construction for
windows, doors, roofing, and structural supports. Its combination
of strength, lightweight, and resistance to the elements makes it
well-suited for building materials.
• Sports and Recreational Equipment: Due to its strength and light
weight, aluminum 6061 is used to produce sports equipment,
bicycles, and recreational vehicles.
• Electronics: The alloy is also used in the production of
electronic housings, heat exchangers, and other components where
heat dissipation and lightweight design are important.
Aluminium 5051,- Al: 95.8-98.3%- Mg: 2.2-2.8%- Mn: 0.1-0.4%- Si:
0.25%- Fe: 0.4% max- Cu: 0.1% max,- High corrosion resistance,
especially in marine environments- Excellent weldability- Moderate
strength,- Clean regularly with mild detergent and water- Avoid
harsh chemicals- Consider protective coatings for outdoor use |
Aluminium 5052,- Al: 97.25% min- Mg: 2.2-2.8%- Cr: 0.15-0.35%- Mn:
0.1% max- Si: 0.25% max- Fe: 0.4% max,- Excellent corrosion
resistance- High strength-to-weight ratio- Good formability and
weldability,- Regularly clean with water- Avoid abrasive cleaners-
Apply anodizing or coatings for extended durability |
Aluminium 6061,- Al: 97.9% min- Mg: 1.0-1.5%- Si: 0.4-0.8%- Cu:
0.15-0.4%- Cr: 0.04-0.35%- Mn: 0.15% max- Fe: 0.7% max- Zn: 0.25%
max,- Excellent machinability- High strength and toughness- Good
corrosion resistance,- Clean with mild soap and water- Inspect
welds regularly- Use lubricants for moving parts to reduce friction |
Aluminium 7075,- Al: 87.1% min- Zn: 5.1-6.1%- Mg: 2.1-2.9%- Cu:
1.2-2.0%- Cr: 0.18-0.28%- Mn: 0.3% max- Si: 0.4% max- Fe: 0.5%
max,- Extremely high strength- Lightweight and strong- Excellent
fatigue resistance,- Regular cleaning recommended- Apply anodizing
or coatings for protection- Handle carefully during machining |
Stainless Steel SS304,- Fe: Balance- Cr: 18-20%- Ni: 8-10.5%- Mn:
2% max- Si: 1% max- C: 0.08% max- P: 0.045% max- S: 0.03% max,-
Good corrosion resistance- Excellent formability and weldability-
Non-magnetic in annealed condition,- Clean with water and mild
detergents- Regular polishing or passivation- Avoid prolonged
exposure to harsh chemicals |
Stainless Steel SS316,- Fe: Balance- Cr: 16-18%- Ni: 10-14%- Mo:
2-3%- Mn: 2% max- Si: 1% max- C: 0.08% max- P: 0.045% max- S: 0.03%
max,- Superior corrosion resistance (especially in saltwater)-
Excellent weldability- Higher pitting resistance,- Regular cleaning
with water- Rinse after exposure to saltwater- Periodic inspections
for pitting and corrosion |
Stainless Steel SS316L,- Fe: Balance- Cr: 16-18%- Ni: 10-14%- Mo:
2-3%- Mn: 2% max- Si: 1% max- C: 0.03% max (lower than SS316)- P:
0.045% max,- Excellent corrosion resistance- Ideal for harsh
chemical environments- Non-magnetic in annealed condition,- Regular
cleaning with water- Avoid harsh chemicals- Consider passivation
for increased corrosion resistanc |
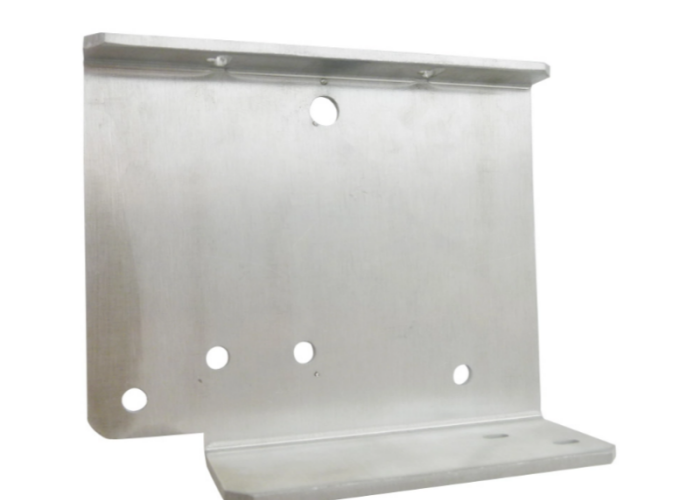
Name: | Aerospace parts |
Tolerance | ISO2768M |
Material | Aluminium 7075 |
Roughness | Ra3.2 |
Surface Treatment | As machined |
About Us



Package
